Ш. М. Гордезиани, первый зам. начальника Главгосэкспертизы России; Я. Г. Френкель, нач. отдела объектов производственного назначения Главгосэкспертизы России; К. Визиковски, старший вице-президент компании «СЕТКО»; В. И. Новак, руководитель отдела углеобогащения компании «СЕТКО»; В. А. Никулин, нач. проектного отдела компании «Коралайна Инжиниринг»; Е. Ю. Семухин, нач. ОФ «Красногорская, ОАО «Южный Кузбасс»; И. А. Пухальский, генеральный директор ОФ «Спутник», ОАО «Шахта Заречная»; В. В. Долматов, главный инженер ЦОФ «Распадская», ЗАО «ОФ «Распадская»; Н. И. Канев, директор ЦОФ «Печорская», ОАО «Воркутауголь»
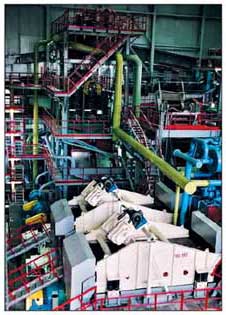 |
Общий вид цеха по выпуску коксующегося концентрата с извлечением до нуля без термической сушки |
В течение 2003 - 2005 годов специалистами отраслевых отделов Главгосэкспертизы России рассмотрены ТЭО и проектно-сметная документация на модернизацию и строительство ряда новых углеобогатительных фабрик в Кузбасском и Печорском угольных бассейнах. Следует отметить смещение акцента в выборе технологии и оборудования для новых проектов в сторону экономической эффективности по сравнению с традиционными подходами, когда основной задачей являлось максимальное извлечение угля в концентрат.
Проекты фабрик разрабатывались институтами с использованием технологических решений зарубежных фирм, таких как финская корпорация «Metso», американская фирма «СЕТКО» и др. Так, обогатительные линии «СЕТКО» внедрены в эксплуатацию на обогатительных фабриках Кузбасса: ОФ «Антоновская», ОФ «Красногорская», ОФ «Спутник», ЦОФ «Распадская», а также на нескольких реконструированных объектах: ЦОФ «Кузбасская», ГОФ «Томусинская», ЦОФ «Печорская». На всех новых фабриках использована замкнутая водно-шламовая схема, отсутствуют какие-либо выбросы в атмосферу, нет термической сушки - самого экологически вредного процесса переработки угля. Фабрики очень компактны, в 2 - 3 раза меньше любой фабрики с аналогичной производительностью, построенной до 2000 года. И в то же время это высокорентабельные производства. Некоторые собственники этих фабрик уже строят новые очереди или проводят реконструкцию по дополнительному увеличению мощности существующих предприятий.
Основным преимуществом проектов «СЕТКО» являются не только технологические ноу-хау, но и применение новейшего импортного оборудования, аналогов которого в России не выпускается. Так, для обогащения шламов кл. 0,15 - 1(2) мм используются спиральные сепараторы из Австралии. Как правило, раньше этот класс обогащали менее эффективно в отсадочных машинах и в механических флотомашинах с применением химических реагентов. При реконструкции ЦОФ «Печорская» установка спиральных сепараторов позволила улучшить работу тяжелосредных циклонов и сократить расходы на флотореагенты. Расход магнетита сократился с 6 кг до 1 кг/т. В случаях, когда целесообразно обогащение «до нуля», теперь применяются пневматические колонные флотомашины, более эффективные, чем отечественные машины других типов, за счет запатентованных аэраторов, позволяющих добиться наименьших размеров пузырьков и наибольшей общей площади их поверхности для максимального извлечения концентрата. Показатели работы таких машин близки к теоретической кривой обогатимости. Как упоминалось выше, для достижения требуемой влажности концентрата всегда применялась термическая сушка. В новых проектах ее заменила осадительно-фильтрующая центрифуга «Декантер» (ОФЦ), которая позволяет довести внешнюю влажность обезвоженного продукта совместно с крупным концентратом до 6,5%, что позволяет свободно транспортировать концентрат в вагонах зимой без смерзания. ОФЦ извлекают в концентрат класс плюс 35 микрон, при этом фактор разделения составляет 500 G. Применяемые износоустойчивые футеровочные материалы (керамика, карбид вольфрама) позволяют машине работать 3 - 4 года без замены ротора. Стоит отметить и импортные вибрационные грохоты с фактором «G» до 4. У отечественных аналогов этот энергетический показатель вдвое меньше, что серьезно влияет на производительность грохота и на эффективность грохочения. Изнашиваемые части импортных насосов изготавливают из высокохромистого чугуна. Срок службы таких частей в несколько раз выше, чем у отечественных аналогов, а регулируемые механически шкивы клино-ременных приводов насосов позволяют быстро и точно настроить водно-шламовую схему фабрики. Для замыкания вводно-шламовой схемы технологи «СЕТКО» применяют глубокие радиальные сгустители с центральным приводом и контролем момента вращения и ленточные фильтр-прессы для обезвоживания осадка сгустителя до транспортабельного состояния. Такая схема исключает необходимость строительства шламонакопителей.
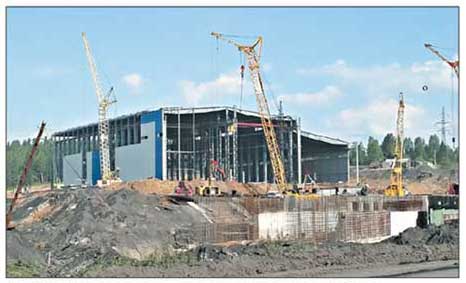 |
Монтаж конструкций корпуса углеобогатительной фабрики |
Причины, по которым на современных обогатительных фабриках пока применяется импортное оборудование, общеизвестны, но главной остается одна: новые технологии с новейшим оборудованием от ведущих мировых производителей позволяют получить максимальный выход концентрата при разумных капитальных затратах и минимальной себестоимости обогащения.
Тесная работа экспертов Главгосэкспертизы, технологов и проектировщиков при рассмотрении проектно-сметной документации, корректировка и уточнение отдельных аспектов, экспертное сопровождение при реализации проектов, без сомнения, позволили обеспечить выпуск высококачественной документации на модернизацию и строительство углеобогатительных фабрик России - важнейшего элемента в топливно-энергетическом балансе страны.
|